Product dimensional drawings
Product dimensional table
(Imperial System)
Installation method
Multiple EXEN direct blasters can be remotely operated with the control panel. If only one unit is operated, it can be in either of manually or electrically.
If the powder likely to cause dust explosion is used in the electric operation, changing the three-way valve to the explosion-proof solenoid valve allows the safe operation.
*If multiple blasters are installed to one air supply source or the aeration is combined, be sure to install the check valves to the air supply side before the solenoid valves, respectively, to prevent abnormal injection owing to decompression on the primary side.
■Calculation of necessary amount of air
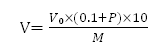
V: Necessary amount of air (L/min (ANR)), Vo: Total tank capacity (L)
P: Operating pressure (MPa), M: Operating cycle (min)
Example) When using six EDB2.5-30 models at an operating pressure of 0.7MPa, at an interval of 5 minutes:

Sufficiently usable with a compressor of 2.2kW.
*Use a compressor with a discharged amount of air of 200L/min (ANR) (1.5kW) or more. If the compressor with 200L/min (ANR) or less, connect the receiver tank of 10L or more just before the three-way solenoid valve.
|